การออกแบบดอกสว่าน PDC ในปัจจุบันในฐานะเมทริกซ์มีความคล้ายคลึงกับการออกแบบเมื่อไม่กี่ปีก่อนเล็กน้อย ความต้านทานแรงดึงและความต้านทานต่อแรงกระแทกเพิ่มขึ้นอย่างน้อย 33% และความแข็งแรงของเครื่องตัดประสานเพิ่มขึ้น γ 80% ในเวลาเดียวกัน รูปทรงและเทคโนโลยีของโครงสร้างรองรับได้รับการปรับปรุง ส่งผลให้ได้ผลิตภัณฑ์เมทริกซ์ที่แข็งแกร่งและมีประสิทธิภาพ
วัสดุคัตเตอร์
หัวกัด PDC ผลิตจากซับสเตรตคาร์ไบด์และเม็ดกรวดเพชร ความร้อนสูงประมาณ 2,800 องศา และแรงดันสูงประมาณ 1,000,000 psi ทำให้เกิดขนาดกะทัดรัด โลหะผสมโคบอลต์ยังทำหน้าที่เป็นตัวเร่งปฏิกิริยาสำหรับกระบวนการเผาผนึก โคบอลต์ช่วยยึดเหนี่ยวคาร์ไบด์และเพชร
จำนวนเครื่องตัด
โดยปกติแล้ว เราจะใช้คัตเตอร์น้อยลงกับบิต PDC แบบอ่อน เนื่องจากคัตเตอร์แต่ละตัวจะขจัดความลึกของการตัดที่มากขึ้น สำหรับการขึ้นรูปที่ยากขึ้น จำเป็นต้องใช้หัวกัดมากขึ้นเพื่อชดเชยระยะกินลึกที่น้อยลง
ดอกสว่าน PDC – ขนาดคัตเตอร์
สำหรับรูปแบบที่นุ่มนวล โดยทั่วไปเราจะเลือกหัวกัดที่มีขนาดใหญ่กว่ารูปแบบที่แข็งกว่า โดยปกติแล้ว ช่วงขนาดมาตรฐานจะอยู่ระหว่าง 8 มม. ถึง 19 มม. สำหรับบิตใดๆ
โดยทั่วไปเราจะอธิบายการวางแนวการออกแบบชั้นวางเครื่องตัดโดยมุมคายด้านหลังและมุมคายด้านข้าง
● คราดหลังคัตเตอร์คือมุมที่ผิวหน้าของคัตเตอร์ปรากฏถึงรูปร่าง และวัดจากแนวตั้ง มุมคายด้านหลังจะแตกต่างกันไป โดยทั่วไปคือ 15° ถึง 45° พวกมันไม่คงที่ตลอดบิตหรือจากบิตหนึ่งไปยังอีกบิต ขนาดของมุมคายของคัตเตอร์สำหรับดอกสว่าน PDC ส่งผลต่ออัตราการเจาะ (ROP) และความต้านทานต่อการสึกหรอของคัตเตอร์ เมื่อมุมคายเพิ่มขึ้น ROP จะลดลง แต่ความต้านทานต่อการสึกหรอจะเพิ่มขึ้นเมื่อโหลดที่ใช้ถูกกระจายไปทั่วพื้นที่ที่ใหญ่กว่ามาก หัวกัด PDC ที่มีคราดด้านหลังขนาดเล็กใช้ระยะกินลึกมาก ดังนั้นจึงมีความดุดันมากกว่า สร้างแรงบิดสูง และอาจสึกหรอเร็วขึ้นและมีความเสี่ยงที่จะเกิดความเสียหายจากแรงกระแทกมากขึ้น
● คราดด้านข้างของเครื่องตัดคือการวัดทิศทางของเครื่องตัดจากซ้ายไปขวาที่เทียบเท่ากัน มุมคายด้านข้างมักจะมีขนาดเล็ก มุมคายด้านข้างช่วยทำความสะอาดรูโดยกำหนดทิศทางการตัดไปทางวงแหวนโดยอัตโนมัติ
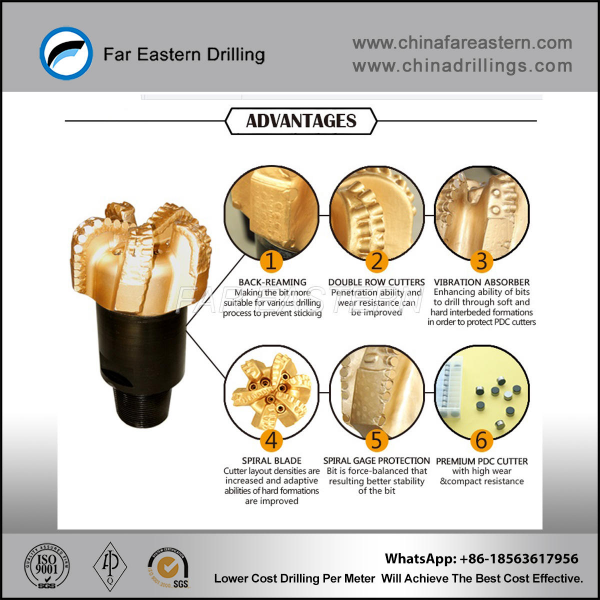
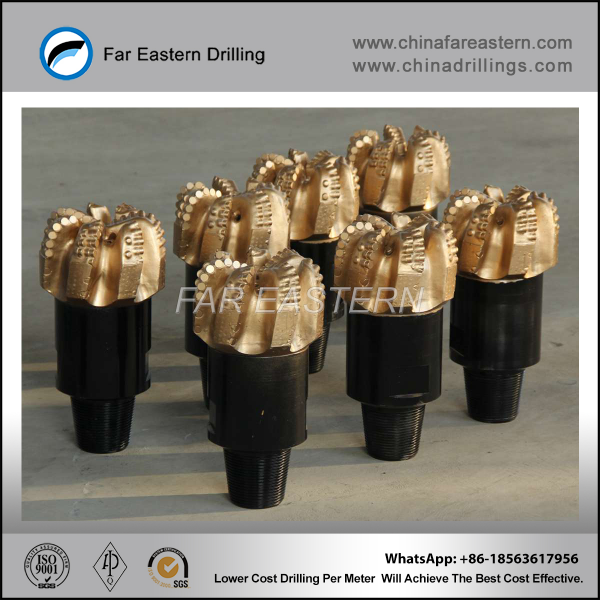
เวลาโพสต์: Sep-01-2023